Robot on tour: "Magic Finger Tip" makes zero clamping systems superfluous
Smart Cobotix is well known as a Universal Robots partner and as a member of the German Robotics Association. Together with partners, the SME has developed a solution that makes cobots on mobile vehicles/robots really mobile, as the following press release makes clear. The price is not known to me, but there should be a market launch price by May 31, 2023. The product is called "Magic Finger Tip" (MFT for short) and is designed for Universal Robots only for now.
- Robot stands on a mobile frame without driven rollers, is moved manually from station to station (location changed).
- Robot stands on a self-propelled industrial truck, an AGV (AGV/ AMR)
- Robot arrives at new station, where the new position is automatically sensed with the MFT. A sophisticated program continuously determines correction values for offsetting with the previously selected coordinate systems. The usual tedious alignment with a zero clamping system or similar is no longer necessary.
- Robot executes its previously learned program again within a very short time after being relocated, without having to be taught at the new station.
- You can call that mobile. Time savings and versatility mean that amortization can be calculated in a whole new way.
Alternative to camera systems and zero clamping systems
The term mobile robotics implies that the robot can be used flexibly at different locations. If it changes its position, it must be precisely aligned at its new location so that it can execute the program it once learned at its new position without errors. Until now, this required complicated zero-clamping systems or very complex and expensive camera technology, which, however, still lacked a decisive detail: the rotation information around at least one axis.
This is where the "Magic Finger Tip" comes in. There is a "Magic Finger Socket" socket provided for this purpose at each workstation. This position was taught once. The "Magic Finger Tip" was assigned a pre-position with a small distance in front of the MFS. When the command comes to search for the position, the "Magic Finger Tip" dips into the "Magic Finger Socket", a calibration run begins, after which the program of the station is run. When the robot returns to this station, it can find its Magic Finger Socket again with a maximum tolerance of 40 mm in the pre-position and execute its program. There is no need for time-consuming coupling and alignment.
What exactly is going on?
After the completion of an automated sequence scheme, a new temporary coordinate system is created. This coordinate system contains all rotation positions of the 3 axes (X,Y,Z). This makes it possible to move a robot from one location to another and have it perform new tasks after the calibration run has been performed. The calibration run includes the detection of an oblong hole by lowering it by a dowel pin. The oblong hole is measured and thus the rotation of the axis that was just selected is determined. The "Magic Finger Tip" with its Magic Finger Socket is only a means to an end here. It is best to put the "Magic Finger Tip" down again after the measurement is complete. An automatic tool changing system, for example from SMARTSHIFT robotics, is recommended for this purpose. The "Magic Finger Tip" is left on the mobile base frame and the working tool can be picked up at the workplace in a changing bag. The "Magic Finger Tip" is used for the calibration. The coordinate system is created with special software. The subsequent real time calculations as well.
The "Magic Finger Tip" is adapted to Universal Robots e-series robots with their force moment sensors. The programming is done in the Polyscope® with the tools from the URcap. The programming of the URcap was done by the company Gräff Robotics GmbH from Hennef.
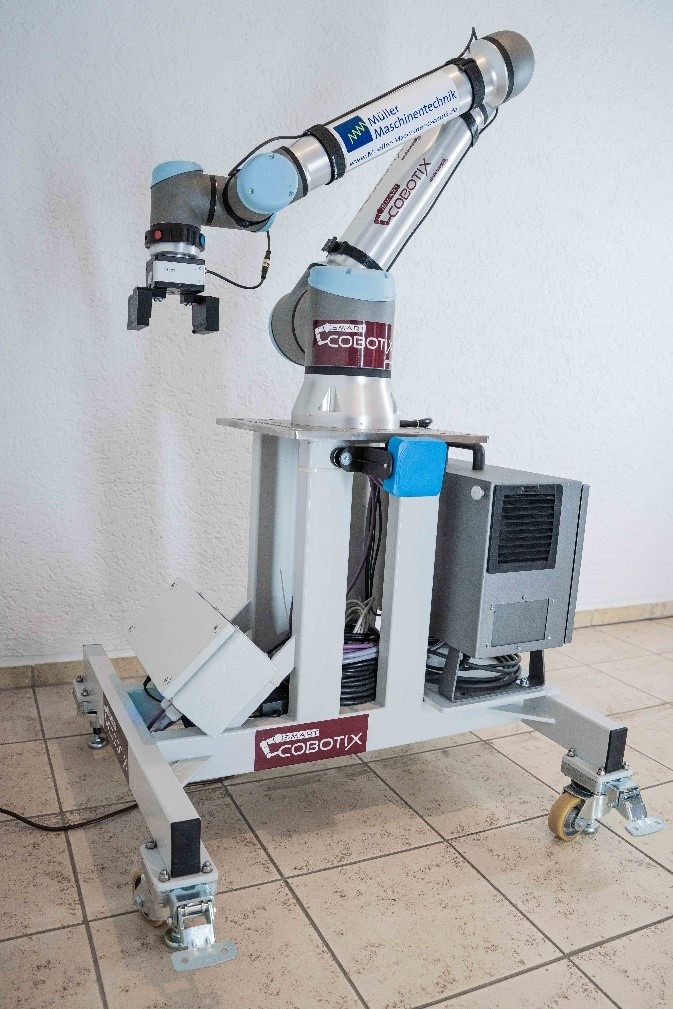
What do you need this system for? 3 possibilities are presented
The 1st possibilityMove manually. Here, the robot is moved manually on its frame to its predefined position. There it then records its coordinates by means of the "Magic Finger Tip" in combination with the "Magic Finger Socket". This means, for example, that the robot reaches almost 100% capacity utilization, minus the short travel and setup time. This is negligible with an automatic or manual changeover system. The robot is no longer tied to a product in the payback calculation. The costs for the mobile unit can be allocated in a mix of different products. Smart Cobotix GmbH offers the mobile trolley, the safety system, robots and as CSI from Universal Robots also a complete integration of the system into your plant.
Customer-specific requirements are of course addressed on a project-specific basis. Smart Cobotix also offers: individual gripper systems, coordinated special functions and automatic tool change systems (electric, pneumatic or both).
The 2nd option: Here, the robot is mounted on an AGV from MiR in Denmark with a manual quick-change system from GRIP GmbH Handhabungstechnik. Flexibility is the trump card. The robot can perform different tasks. In this case, the "Magic Finger Tip" is changed manually in order to be able to perform a job with a different tool.
At BLEICHERT Automation in Osterburken, the robot mounted on an omnidirectional BLEICHERT FTS was equipped with an automatic tool change system from SMARTSHIFT robotics in Norway. The work tool, a common finger gripper, was located in the tool holder at the static work station. The MFT is carried in the tool holder on the vehicle. After calibration, the "Magic Finger Tip" is placed on the mobile side and the gripper is picked up on the stationary side. When the work is finished, the gripper is deposited there again. The AGV can move independently to the next station. There is constant interaction between the robot and the AGV. Both systems are coupled in terms of safety.
The 3. possibilitypossibility of the "Magic Finger Tip" is the calibration of the AGV. If the robot is on the fixed side and the Magic Finger Socket is on the AGV, a tightly toleranced KLT or blister, for example, can be filled safely even if the AGV is not exactly at the right angle or distance.
In the course of further development, the system will be expanded to include an RFID reading and writing unit. Finally, a special camera will be used, which will considerably expand the tolerance range for finding the Magic Finger Socket. Have you realized what unimagined possibilities the Magic Finger Tip opens up? Mobile welding carts, mobile screw units, so many other mobile possibilities due to shortest changeover times and precise adjustment between new location and first time program.
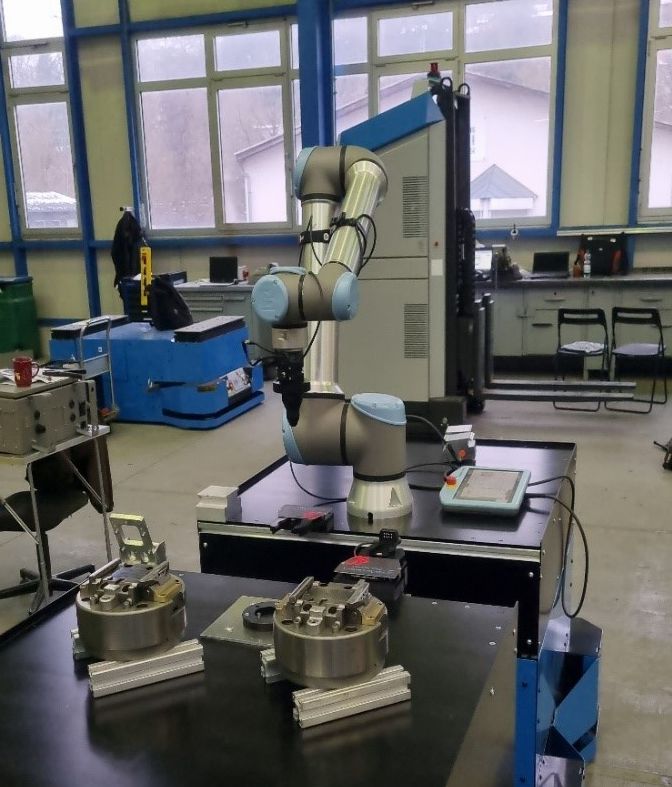
Are we networking? LinkedIn
-> Go to the Cobot group on LinkedIn (link). The author is also a consultant (robotics, tech & finance). Hardly anyone is likely to have a comparable market overview.